The legendary Tony Levin shows his limited edition King Crimson intaglio print collection at the Haggin Museum on Feb. 16, 2023. Learn More about this high-quality print collection here:
https://timeless-prints.com/tony-levin-king-crimson-fine-art-prints/
Category Archives: solar plate printing
Fifteen Year Challenge for Finer Polymer Photogravure Prints
When I first put my procedure for making and printing polymer photogravure plates online in 2006, it was after a few years of my own frustrations in the process. I posted it in response to a lack of comprehensive information about the subject as it pertained to creating continuous tone images for photography. The traditional printmakers weren’t concerned with it, and the computer nerds (of which I am one) didn’t have any meaningful elbow grease or track record when it came to making traditional intaglio prints.
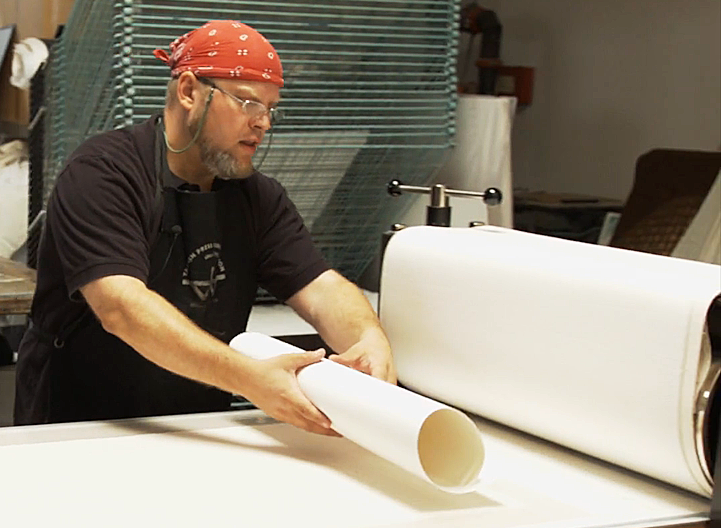
Picking up where others’ work had left off, I created a custom workflow and process compensation curve to accommodate a finer, higher-resolution aquatint screen than anyone else was using at the time. Our screen is 2-3 times as fine as traditional rosin dust used for aquatinting copper photogravure plates. At 1200 dpi, our fine, third-generation, heavy-duty aquatint screens with custom stochastic pattern are a double-edged sword. We don’t sell them to the public because they are less forgiving than coarser screening processes, but yield superior, fine continuous tones for photogravure when handled and used under a controlled environment using the tried-and-true KM73/83 plates by Toyobo, for which our screens and system for making continuous tone plates was designed.
While excellent technical books on polymer platemaking and creating digital negatives for contact printing are now available, there were but a few good ones in 2004. The only one most of us referenced was written by digital negative pioneer and process wizard Dan Burkholder. Today, faster methods to getting inkjet-quality photogravure prints from polymer, such as Direct-to-Plate (as taught by printmaking instructor Don Messic) and reliable, open-source software for calibrating your printer drivers for making custom digital negatives now exist.
While direct-to-plate (DTP) is easier and faster to teach polymer plate making certainly, it does not employ a critical, secondary aquatint layer to create the proper plate texture and variable depths. This is what gives photogravure its unique 3D qualities, otherwise you’re just printing a flat inkjet print that’s been transferred flatly to a plate. This critical aspect of plate depth and ink relief is among the most apparent qualities in traditional photogravure prints – when made on on finer, Asian, gampi papers, in particular. While hard to demonstrate in a digital image, the look of a traditional copper plate photogravure, when executed properly, is unmistakable.
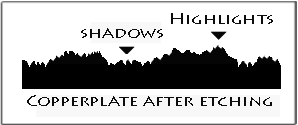
Illustration by Peter Miller
While DYI is all the rage, some artists need an experienced, dedicated technical collaborator who understands their goals. Finding someone who has an intimate knowledge of the photo mechanical process as well as intaglio printing itself, is still the same today as it was 150 years ago. Finding such an experienced artisan is certainly harder than it was way back then.
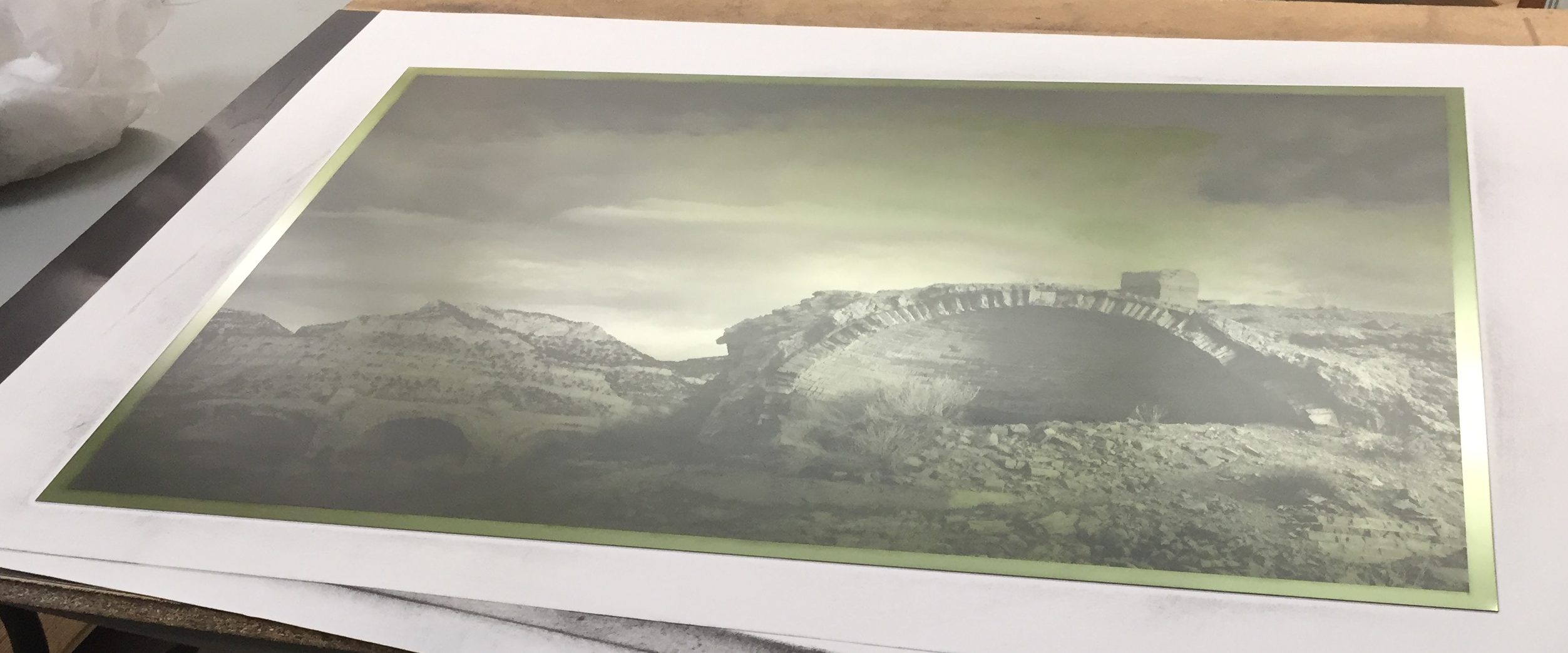
As far as process and workflow, not much has changed at Intaglio Editions in our 15 years working with artists, clients, and their collaborators. We still create custom plates to meet client specifications including plates crafted for a specific ink color. In proofing the work with the client to refine the nuances and going back to the digital file and reshooting plates as needed, we have been able to provide the optimal prints our clients demand for their fine art projects. What has changed since the early 2000s is our ability to branch out into new territory, following the traditional processes, bringing the use of polymer even closer to the look (and literal feel) of traditional copper photogravure, without the added toxicity and expense.

What makes Intaglio Editions Premium Photogravure Plates different is our custom, high-resolution aquatinting process, and our ability to offer extra large pre-made plates up to 23″ × 39″ (among the largest commercially available). While other methods are limited in size and often leave tell-tale “salt-and-pepper” grain in their photogravures, our traditional double-exposure method creates a more authentically etched plate and print, but at a price. It is more time-consuming and requires more steps and attention to detail than other methods.
So why do we do it? This extra work our process requires follows closer to traditional platemaking methods and gives our custom plates the edge, literally. Unlike newer plate processes, the surface of our plates have detail and textures can be felt by the fingertips. This demonstrates how we provide the smoothest continuous tones possible with this process more in keeping with traditional photogravure plates. Our plates and prints have been praised by artists, photographers and printmaking experts worldwide for their fine nuances, smooth tones, and shadow detail.
Intaglio Editions continues to offer the photogravure-quality plates we use in our printmaking to professional artists and printmakers who love making rich, photographic prints, but who may not be interested in becoming expert platemakers as well. This helps our friends and customers get faster results, and helps them achieve that last stride of excellence that so often eludes newer plate makers, or those new to photogravure printmaking.
New and experienced printmakers alike may want to take advantage of our long-standing $99 Trial Plate offer. We’ll create an 8″ × 11″ plate of your custom image using our custom, double-screened, high-rez platemaking method for just $99, to see if our plates don’t provide the smoothest, richest continuous tones you’ve ever seen from this process. Shipping, handling and customs, duties, or other fees will apply. Our Premium Photogravure Plates and other customer services are available at the Intaglio Editions Shop.
Newton Rings and Contact Problems

Newton Rings and Contact problems between the film positive and plate cause these white patches in the print.
Hi Jon,
I’ve been making plates for several years for my photography work and have only recently started having a problem with those dreaded spots on the plate and subsequently the prints. In researching the problem I came across your web page and it was the ONLY place I have seen a reference to these spots. I tried you suggestion of drying the transparency and then did a small 4×5 transparency of the image on plate and it seemed okay, but then when I did an 8×10 transparency with the same process, the plate had the dots again.
Do you have any further advice about this problem with Pictorico film? Or another film that might work without the problem. It’s maddening and I’ve lost several days of work and lots of plates trying to resolve it with no luck.
I have some Sihl film I’ve never used and considering it. Anyway, any help you could offer would be very appreciated. I know Dan Welden and he says it’s a problem with Pictorico. Is there a work around?
Thanks so much,
Hi Jari,
It is much easier to be successful with smaller plates. Larger plates have a learning curve all their own since it is a larger surface area, making tight, contiguous contact with the plate more difficult.
The problem of dark spots (which become white in the print) is typically a contact problem. In some cases it can be attributed to newton rings,. In most cases it is simply a lack of contiguous contact where the film is able to go out of focus and become diffuse in places, weakening the density in the plate in those specific areas.
Newton rings can occur between the glass of the vacuum frame, and film – or between the film and the plate. I avoid newton rings on top by using Kreene plastic instead of glass in my vacuum frame.
Two other solutions to avoiding newton rings with larger plates:
1. Pictorico now makes a textured film. The texture creates small cracks where air can escape, avoiding the newton ring issue on some level.
2. The other solution is to apply baby powder finely to the plate and/or film positive prior to the second exposure to the plate. I use it sparingly, and remove as much as possible with a hake brush before putting in the vacuum frame. It does the trick.
Hope that helps. LMK if you have any further questions and best wishes for your project!
Jon Lybrook